Understanding GRP Housing Prices and the Growing Business Landscape of Composite Materials
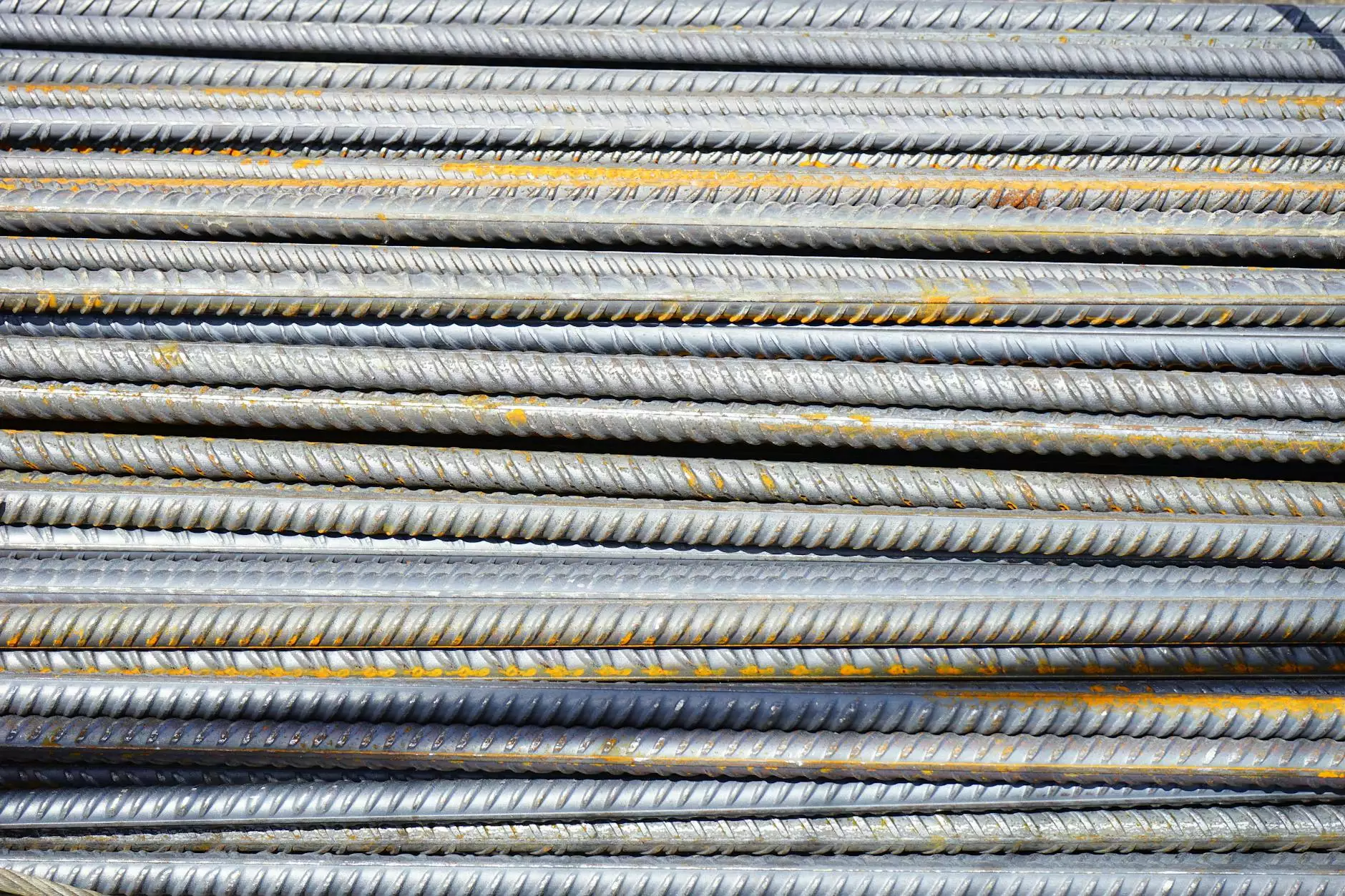
In recent years, the global construction and manufacturing sectors have experienced a transformative shift driven by innovative materials that offer superior durability, sustainability, and cost-effectiveness. Among these advancements, Glass Reinforced Plastic (GRP), also known as fiberglass, has emerged as a preferred choice for a wide range of applications, including housing solutions, industrial components, and specialized infrastructure.
What Are GRP Housing and Why Are They Gaining Popularity?
GRP housing refers to structures manufactured using glass-reinforced plastic composites. These structures are celebrated for their lightweight nature, resistance to corrosion, low maintenance requirements, and excellent aesthetic qualities. Over the past decade, the demand for GRP housing has surged, driven by both economic and environmental considerations.
The Advantages of Using GRP in Housing
- Cost-Effectiveness: Lower manufacturing and installation costs compared to traditional building materials.
- Durability and Longevity: Excellent resistance to weathering, corrosion, and UV damage, ensuring long-lasting structures.
- Lightweight Yet Strong: Easier to transport and install, reducing labor and logistical costs.
- Design Flexibility: Ability to mold into complex shapes and customizable architectural features.
- Environmental Benefits: Reduced material waste and recyclability contribute toward sustainable building practices.
Market Dynamics Shaping the GRP Housing Prices
The pricing of GRP housing is influenced by a confluence of factors, ranging from raw material costs to technological advancements and market demand. Understanding these variables is essential for investors, manufacturers, and consumers alike looking to navigate this growing industry.
Key Factors Impacting GRP Housing Prices
- Raw Material Costs: The price of resin, fiberglass, and other composite components directly affects the overall cost of GRP structures. Fluctuations in chemical feedstock prices can cause variations in production costs.
- Manufacturing Technology: Advanced manufacturing processes, such as automation and precision molding, may initially lead to higher capital investment but often reduce long-term costs and improve quality, influencing market prices.
- Supply and Demand: An increase in construction projects adopting GRP solutions elevates demand, which can drive prices upward, especially in regions with limited manufacturers.
- Regulatory and Environmental Policies: Governments promoting sustainable building materials may subsidize or incentivize GRP use, impacting market prices favorably.
- Scale of Production: Larger production volumes typically lead to economies of scale, reducing unit costs and thereby lowering GRP housing prices.
- Design and Customization: Complex designs or bespoke structures may incur additional costs, influencing the final price.
Current Trends and Future Projections for GRP Housing Prices
The phenomeon of rising GRP housing prices is interconnected with global economic trends, technological innovations, and the push toward sustainable infrastructure. Currently, market analysis indicates that prices are gradually rising but remain competitive relative to traditional materials like concrete and steel.
Forecasts suggest that as manufacturing processes become more efficient and supply chains stabilize, GRP housing prices are poised for gradual decreases, making them an even more attractive option for residential, commercial, and industrial projects. Additionally, as governmental regulations favor greener materials, increased incentives could further influence pricing dynamics in favor of GRP solutions.
Business Opportunities in the GRP and Composite Materials Sector
Businesses involved in the STP (sustainable, technological, and production) aspects of composite materials are poised for significant growth. The market for shielding structures, transportation components, and housing solutions is expanding rapidly, supported by innovations and increasing acceptance across sectors.
How Companies Can Capitalize on the Growing GRP Housing Market
- Invest in Advanced Manufacturing: Modern machinery and automation can enhance production efficiency, reduce costs, and allow customization, boosting competitiveness.
- Focus on R&D: Developing new formulations for resin and fiberglass that improve strength, weather resistance, and ease of installation can create unique selling propositions.
- Expand Design Capabilities: Offering architectural flexibility and bespoke solutions can attract premium clients seeking innovative housing solutions.
- Build Strategic Partnerships: Collaborate with construction firms, real estate developers, and local authorities to secure large-scale projects.
- Prioritize Sustainability: Meeting environmental standards and promoting recyclable and eco-friendly products position a company as a leader in responsible manufacturing.
Role of Celtic Composites in Shaping the GRP Housing Industry
Celtic Composites stands out as a pioneering enterprise committed to delivering high-quality, innovative ROC (Reinforced Organic Composite) solutions tailored to the needs of modern housing infrastructure. With a focus on research, manufacturing excellence, and client collaboration, Celtic Composites actively contributes to reducing GRP housing prices through efficient production and technological advancements.
The company’s strategic emphasis on sustainability, quality control, and market expansion aligns perfectly with the growing demand for cost-effective and durable housing materials. By investing in state-of-the-art manufacturing facilities and nurturing a dedicated R&D team, Celtic Composites ensures their components are at the forefront of industry standards.
How the Future of Business in GRP and Composites Will Evolve
The future trajectory for businesses operating within the GRP and composite materials space is promising. As infrastructure demands evolve and environmental considerations become more central to construction practices, the industry will experience technological breakthroughs and market expansion. Some anticipated developments include:
- Automation and Digital Manufacturing: Adoption of Industry 4.0 concepts will streamline processes, reduce costs, and improve quality control.
- Sustainable Material Innovations: Development of bio-based resins and recyclable fiberglass composites will meet eco-friendly standards and appeal to a broader market.
- Global Market Expansion: Emerging economies and urbanization trends will increase the demand for affordable, durable, and lightweight housing solutions.
- Smart and Modular Housing: Integration of smart technology and modular design approaches will revolutionize construction practices using GRP and composites.
Conclusion: Embracing the Opportunities in GRP Housing Prices and Business Growth
The landscape of GRP housing and the wider composite materials industry is vibrant with opportunities. As industry leaders like Celtic Composites continue to innovate and adapt to market currents, the prospects for affordable, sustainable, and high-performance housing solutions are more promising than ever. With understanding market dynamics, technological advancements, and strategic business planning, stakeholders can capitalize on this growth trajectory to maximize profitability and contribute to environmentally responsible infrastructure development.
In summary, tracking GRP housing prices is critical for investors, builders, and consumers seeking cost-effective yet durable housing options. Simultaneously, recognizing the trends and innovations shaping the industry will enable business entities to position themselves ahead of the curve, fostering success in this rapidly expanding sector.